
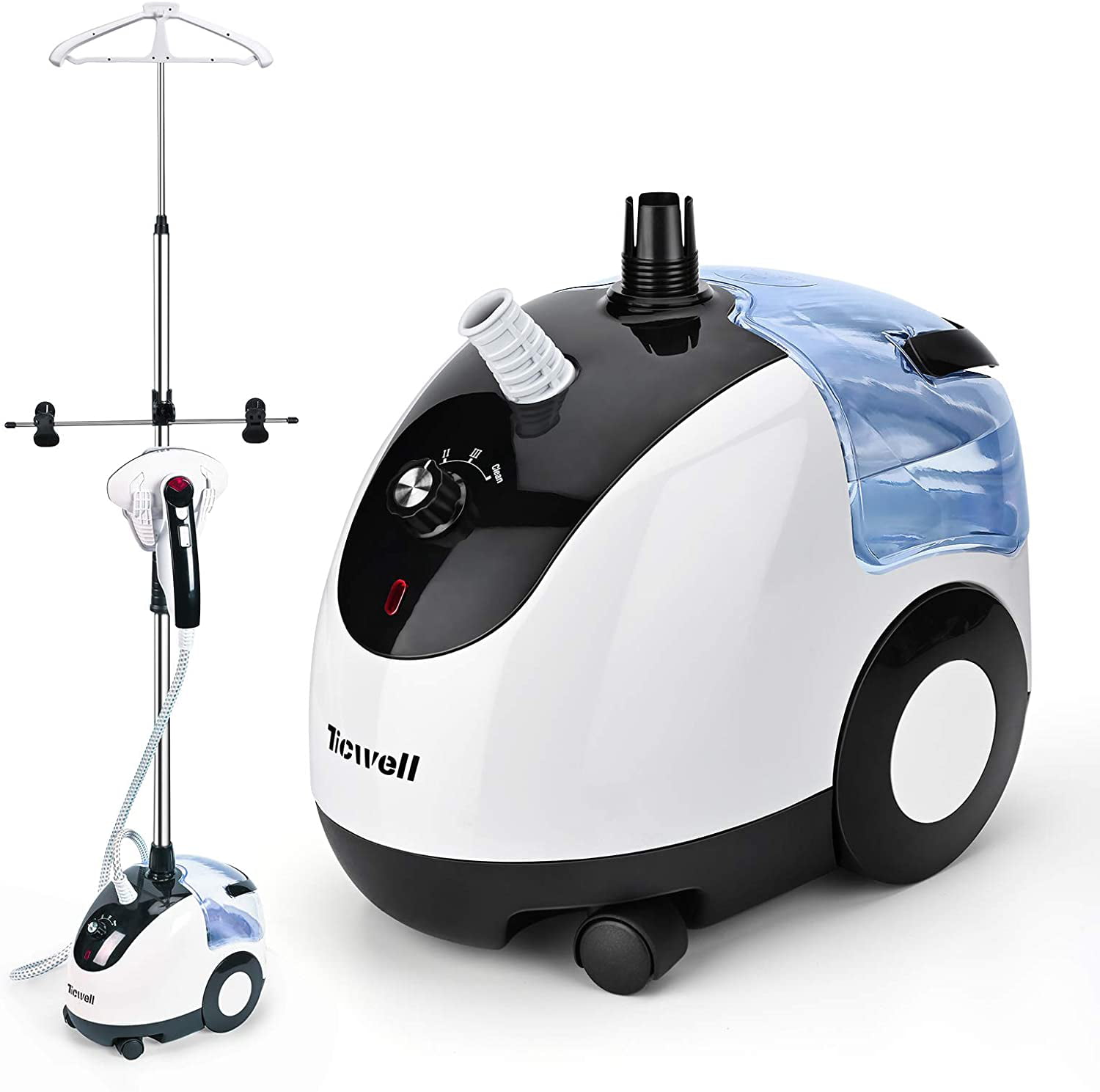
This contributed to environmental contamination, and much potentially reusable PCE was lost to the atmosphere. Machines of this era were described as "vented" their drying exhausts were expelled into the atmosphere, the same as many modern tumble-dryer exhausts. At this time, dry cleaning was carried out in two machines-one for the cleaning process and the second to remove the solvent from the garments. This cycle minimized the risk of fire or dangerous fumes created by the cleaning process. A drop shop receives garments from customers, sends them to a large plant, and then has the cleaned garments returned to the shop for collection by the customer. Infrastructure įrom the customer's perspective, dry cleaning businesses are either "plants" or "drop shops". Because it is stable, tetrachloroethylene is readily recycled.

It has excellent cleaning power and is nonflammable and compatible with most garments. Shift to tetrachloroethylene īy the mid-1930s, the dry cleaning industry had adopted tetrachloroethylene (perchloroethylene), or PCE for short, as the solvent. These solvents were much less flammable than petroleum solvents and had improved cleaning power. After World War I, dry cleaners began using chlorinated solvents. The use of highly flammable petroleum solvents caused many fires and explosions, resulting in government regulation of dry cleaners. įlammability concerns led William Joseph Stoddard, a dry cleaner from Atlanta, to develop Stoddard solvent (white spirit) as a slightly less flammable alternative to gasoline-based solvents. He opened the first dry-cleaners in Paris in 1845. Jennings referred to his method as “dry scouring”.įrench dye-works operator Jean Baptiste Jolly developed his own method using kerosene and gasoline to clean fabrics. The expression "dry cleaner" is used both for the shop providing dry cleaning service and for the operator of the machine that performs the process.ĭry cleaning originated with American entrepreneur Thomas L. Most natural fibers can be washed in water but some synthetics (e.g., viscose, lyocell, modal, and cupro) react poorly with water and must be dry-cleaned. Alternative solvents are 1-bromopropane and petroleum spirits. Tetrachloroethylene (perchloroethylene), known in the industry as "perc", is the most widely used solvent. These Quick Clean Cleaners are molded with an antistatic material and use a novel dry cleaning strand that gently sweeps and removes harmful contaminants from the connector without damaging the connector end face.Dry cleaning is any cleaning process for clothing and textiles using a solvent other than water.ĭry cleaning still involves liquid, but clothes are instead soaked in a water-free liquid solvent (usually non-polar as opposed to polar water).
#Clothes quick cleaner Patch#
The Fluke Networks Quick Clean Cleaners are a family of mechanical cleaning tools designed to clean fiber optic connector end faces on patch cables, within adapters or patch panels. The Quick Cleaner family is specifically designed to provide a cost effective solution for most bulkhead connectors and end-faces, including MPO/MTP connectors. These cleaners are great complements to the existing Fluke Networks fiber optic solvent pen, cleaning cube and cleaning kits for all fiber environments. Even with no training, field technicians and fiber installers can use a simple insertion and push motion to remove residue, debris and dust that can negatively impact network performance. With Fluke Networks Quick Clean™ Cleaners, harmful contaminants are easily removed from a wide variety of connector types. Research has shown over 85% of fiber related problems in data centers, campus, and other enterprise or telecom environments are caused by contaminated connectors or end-faces.
